Webinars
Upcoming
April 15, 2025 11 am CT (12pm ET) (Click To Join)
Aerodynamic Study of Boeing 737-800 and Truss-Braced Wing Aircrafts Using CFD Techniques
Md Mashiur Rahman, Tennessee State University
This research aims to study the aerodynamics of a simplified Boeing 737-800 aircraft using the ANSYS Fluent Computational Fluid Dynamics (CFD) model and to design an aircraft with a higher lift-to-drag compatible with Carbonless Electric Aviation. The ANSYS FLUENT is a high-fidelity CFD model that can be reliably used to simulate aircraft aerodynamics and compare them against any observed data. The study focuses on the flow characteristics and turbulence properties around the aircraft, lift force, drag force, and the drag polar of the aircraft with different angles of attack. Field data collected from pilots of Boeing 737 are used to benchmark the CFD results. Model validation was done using the ONERA M6 wing, a standard NASA model with published data and results. A good comparison confirmed the mesh quality, boundary conditions, and physics choices. Once the validation was done, the Boeing 737-800 CAD model was created. A refined mesh was created with a y-Plus value of less than 10. Mesh independence was verified. Different turbulence models were tried, and K-w SST was determined to be ideal for the study. The results of this study demonstrated a reasonable comparison of drag polar with the literature results and the lift-to-drag ratio (Cl/Cd) with pilot data. The pilot data indicates a Cl/Cd value of 13.45, while our CFD results yield 13.49 at an angle of attack (AoA) of 2.5 degrees. Both Cl and Cd increase with AoA within the range in the present study, which is expected. The overall agreement between these values validates the accuracy of our CFD analysis. Once the aerodynamic study of the baseline Boeing 737-800 model was completed, CAD models of a few truss-braced wing models with different aspect ratios were created and run in ANSYS Fluent. Some of those results will be presented in the webinar.
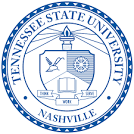
Archived
A Comprehensive Optimizer for Multi-Objective and Multidisciplinary Applications
Axial Fan Optimization for High-Bypass SOFC-C-GT Hybrid System
An Exploration of Ammonia NOx Emissions Using CFD
Tennessee Tech
University’s Pressurized SOFC Test Stand Updates and Progress Through 2024
Investigation of Ammonia Fed SOFCC-GT Hybrid System for Commercial Aviation
Design and Manufacture of an Anode Ejector to Boost System Efficiency of a 1kW SOFC
Zero/Low Emission Commercial Aircraft Powered by Solid Oxide Fuel Cell Turbogenerator Hybrid
Design and Operation of Solid Oxide Electrochemical Cell Systems for Space Applications
SWaP Analysis and Optimization for SOFC-C Hybrid System for Commercial Aviation
Modeling of a SOFC Combustor Hybrid Cycle for Commercial Electric Aviation